How to home-build a Moth - James Sainsbury's step-by-step guide!
by James Sainsbury 29 May 2020 21:30 BST
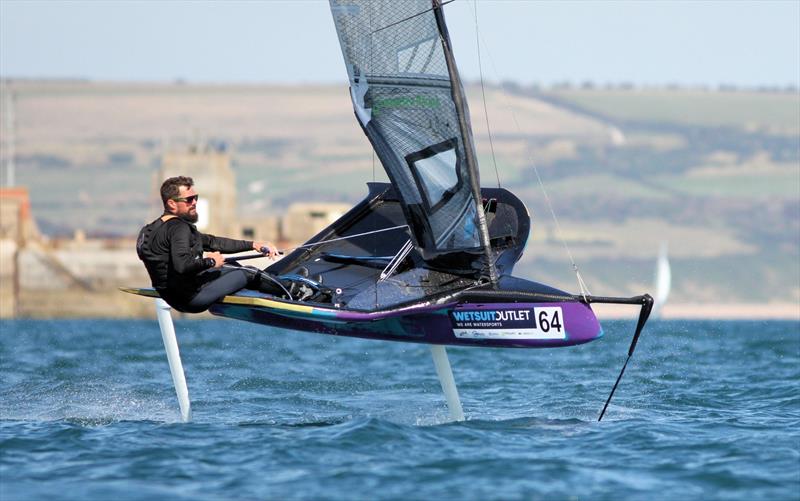
James Sainsbury sailing Valkyrie © Mark Jardine
Since building my boats I have had many questions about how I went about certain areas of my builds. Below are the ways that I have built my last two International Moths. These are the basics, and I am sure there are better ways, but building in your living room is a little different to a proper workshop.
Key items to think about - before you start!
- Fixed or removable wings
- Solid or cloth wings
- Male mould or female mould
- Hull shape / characteristics
- Any crazy ideas!
Design
Work out your design, I did not have CAD...
- I took measurements every 30-50 cm from current boats, but it depends on how exact you want your plans to be. Overlay them on to some gridded paper with a scale you will understand.
- Draw your own design over the top. This will give you your measurements to work from when building your mould
Mould
There are two different processes below. I used both on different boats, the first one is definitely my preferred method when I build another!
Process One:
- Cut MDF ribs matching measurements from your drawing
- Join these all together with a spine running bow to stern, top and bottom, and fix to a board as a base
- Fill the voids between the ribs with solid foam insulation - ensure it is a tight fit, or hold in place with something (I used long kebab sewers).
- Shave the foam down to the same level as the ribs. Take great care where the hull curves as you do not want to take too much away.
- Once you are happy with the shape you can then fill any small voids you have
- After this, using lightweight fibreglass e.g. 80-100 gsm, cover your mould with two layers - this will give it some protection from dents and scratches, plus a solid skin to work from.
- Once set, sand it flat. If there are any imperfections then sand/fill them, as they will show when you come to make your mould.
- Cover in release tape (I used parcel tape). Make sure there are no creases in it.
- Cover in release agent, as specified by the product you are using.
Or, Process Two:
I used Layered solid insulation foam, the thickest I could find. No CNC machine for me.
- Ensure silver foil / paper backings is removed - it's frustrating but much easier when it comes to shaping your hull.
- Fix the foam blocks together, I used long kebab sticks at angles to hold it all together, glues did not form a permeant enough bond.
- Draw your centreline onto the top of the foam. Be gentle with the foam as it dents and scratches easily, I used a sharpie for all my drawing onto it.
- Use this centre line to measure and mark your outer hull shape onto the foam. Ensure that the mould is a little over length in the stern to help later, I just did this on one side to start with. The important thing here is to have decided if you are using a male or female mould. If you are using a male mould you will need to subtract all you measurements by the end hull thickness.
- Cut this shape vertically down the foam. This will give you your maximum hull width shape front to back. A large kitchen knife and a surform are you friends.
- Next you need to draw the rocker into your mould. Assuming that the deck level of your boat is flat, measure from the bottom of the foam up, and mark using your measurements from your drawing.
- Cut horizontally to the centreline. Now you should have a very square hull shape, but with your largest dimensions.
- Now comes the fun bit! Depending on how technical your drawing was you may have some interim measurements to work with - however I did all my hull shaping by eye, cutting and shaving the hull down to the shape I had pictured. Be mindful to do a little at a time.
- A bendy straight edge is useful here - draw vertical lines down from your initial marks on the centre line. This will show you the contours of the hull.
- Keep sanding and drawing until your end up with your desired shape. This takes a lot of time.
- Once you are happy with the fist side of you boat, repeat numbers 4 & 5 on the other side of the mould.
- At this stage, I made some cardboard guides from the side I have already created to help me in shaping the other side. Make sure these are as accurate as possible or you will end up with a wonky boat.
- Spend time ensuing your boat sides match. Do not rush it - the more complicated the shape, the longer it will take.
- Once you are happy with your shape, cover your mould with two layers of lightweight fibreglass 80-100 gsm. This will give it some protection from dents and scratches, plus a solid skin to work from.
- Once set, sand it flat. If there are any imperfections sand / fill them, as they will show when you come to make your hull/mould.
- Cover in release tape (I used parcel tape) make sure there are no creases in it.
- Cover in release agent, as specified by the product you are using.
Building A Female Mould:
- Ensure that the male mould is well coated in release agent as this will save a lot of hassle later.
- Cover your mould in 2 layers of lightweight 100g fiberglass and wet through with resin.
- Add more heavy weight fibreglass - the more layers you put, on the stiffer and better the mould will be.
- Build braces into you mould so that it will hold its shape and sit upright when done
- Once you feel you have a solid mould, try and release the male from the female mould. Use small wedges to help pop it out.
- Once released clean the female mould, ensuring that you have a clean surface to work with.
- Fill and smooth any areas that may need it and then paint with a strong paint.
- Compound and polish. The shinier it is, the easer the final hull will come out.
- Once happy with the finish cover in release agent.
Building A Hull:
- Take time in preparation:
- Cut all bagging materials;
- Cut all hull materials;
- To reduce risk I laid my hull up in three stages. It uses more consumables but ensures you do not run out of resin pot life, etc.
- Using a male mould, I would lay and tape Peel Ply loosely to the mould, wet it out with resin, lay one layer of 200g of biax carbon +/- 45 on the centreline, ensure wetted thoroughly, Peel Ply over the top, and vacuum down until set.
- Once set, remove bag and Peel Ply, mix up resin with mirco balloons in it to form a thin paste, then spread over your carbon on mould and foam sheets. Lay foam onto mould, tape or tack in place with small nails or staples, add a layer of Peel Ply, then vacuum again.
- Once this has set, remove from bag and Peel Ply, ensure surface is smooth, then wet foam out with resin. Lay one layer of 200g plan at 0 degrees of centreline, Peel Ply and vacuum.
- Once this has set, remove from bag and carefully from mould (sometimes easier said than done).
- You have a hull!
Bulk Heads / Transom:
Moths require that you have two buoyancy compartments, so you will need a full bulkhead in the location of your king post. This will provide your two tanks and an important strengthening location.
- Make up a large carbon flat sheet - you will cut your bulkheads from this. Ensure Peel Ply is used both sides, this will help bonding to other parts later. My lay up is biax one side +/- 45 and plain on the other side at 0, 5mm foam core.
- Make a cardboard template for where you want bulkheads or strengthening in your hull. In my boat, I have one under the king post; one from king post area to bow of boat; two half-depth ones under the area I will be running across; and, one under the rear wing bars. I try to incorporate the front wing bar into the main bulkhead.
- Once the cardboard templates are made, transfer these to your pre-made carbon sheet. Try and lay them out to minimise wastage.
- Check their fitment, but do not glue them in yet - just tape them in for reference.
Main Foil Case:
Make a tapered mould for your case. I have made both of mine slightly oversized so I can make small inserts / packers for foils at a later date. When making the mould use foam as it is easy to break apart once done.
- Make mould shape. Slightly taper so it is longer at the top, also make it longer than needed. Wrap in release tape and release agent.
- Cut carbon so you have ten pieces that will just wrap from one side round to the other, both front and back. Ensure that some are plain on 0 degrees and others are biax +/-45.
- Wet out all of the carbon - lay sides alternately, this way it will form a strong case once set. Your sides will be thinner but you will have extra strength front and back for the inevitable knocks it will receive while sailing. Vacuum bag until set
- Remove from bag and chip the foam mould out from inside.
- Measure where it is going to sit in the hull and remove the inner biax and foam in this area, plus an additional an inch as you will eventually carbon it on the outer hull skin. Once all excess foam is cut away mark in where the case will sit. Again do not glue in.
- Make up a set of carbon sandwich bracers to fit either side of the case, these will support it against the hull and the deck once on.
Fixed or removable wings? This determines the next stages of your build.
Removable Wings:
- If you will be making your front and rear sockets out of tubing you need to determine the angles of your wings rising up, but also fore/aft angles to cut the join so the port and starboard tubes fit perfectly together.
- Make a jig to hold the tubes, as the next stage is to glue them together.
- Once glued they will need to have carbon wrapped around the joins, this is not an area to skimp on. Place multiple layers of Unidirectional over the join, with a good overlap on the tubes. Taper the overlap so you end up with a tapered finish. Include a couple of layers of biax in the layering to help with twist, either vacuum bag or shrink tape to compress while setting.
- Cut hull where required to fit sockets. Do not glue in yet...
- Use new sockets to build wing bars and joints to outer bars. Make sure continual measurements are taken as you want to be as close to maximum width as possible but not over it!
Fixed Wings:
- Use the blue modelling foam to shape front and rear wing bars to desired shape.
- Wrap in 4 layers of 300 unidirectional, alternated with +/- 45 biax.
- Pour acetone into the end of your wingbar and let it melt the foam away.
- Make some joiner inserts made from carbon sandwich that will join either side together. Try and get them as far up the bars as you can as this will help with strength towards the end of the wing.
- Make some outer wing bars to join the front and rear bars together (this could be tube if you wanted).
- Fill the void in your frame with foam, glued together and to the frame.
- Then lay the carbon on either side - I did mine one side at a time as it was such a large area. One layer across the whole surface and another layer covering the main area I was going to be moving on to, to help support the foam.
- My deck fairings were carved from foam which I taped over so I could then lay carbon. The amount of carbon used depended on where it was positioned or its need for strength vs. use as a mould to then dispose of. Most fairings are 2 layers: one biax one plain weave.
King Post Area:
At this point some critical processes are going to take place, you are going to tie you front wing sockets into the king post which will all marry up to the hull and full bulkhead.
- Set sockets into hull and securely tape so they will not move - your king post is going to sit on top of this.
- Your king post needs to be set between 7-10 degrees backwards to aid the kicker angles.
- Cut the bottom of the king post to fit the top of the sockets closely and then glue in place.
- As with the socket this needs to be wrapped in carbon to hold it to the sockets.
- Are you going to have compression struts? Most boats are going away from this now so more material needs to be added to front wingbars to help with the extra strain. Carbon I beams are inserted into the tube sections to aid with this.
Kicker Strop Tube:
- Find a piece of hose / tube or something rubber that will soften up when warm (you see why later). Ensure it is long enough to wrap around you king post plus some extra inches to tape together. Cover in release agent.
- Cut some lengths of plain and biax carbon - wrap these around the tube, wrap in plastic, fold around king post and tape in place as low as it can go.
- Once set, slide it off and remove the plastic, then rough the new tube up with sandpaper.
- Glue in place, then carbon it into the king post and wing sockets. Vacuum it all down (make sure the hose, wing sockets and king post ends are exposed from the bag or it will go wrong...).
- Once set, remove from bag. It's now time to get the hose/tube out. Boil the kettle, make a coffee, and use the remainder of the boiling water to pour slowly down one end of the tube. Once it is hot and flexible, get a set of pliers and give it a pull and twist and it should slide right out.
Bowsprit / Pushrod Tube:
- Decide how your bowsprit is going to fit into the bow of the boat.
- I used a little extra tube here that I glued onto the hull that holds the pushrod tube. I used a large diameter that the bowsprit then slots into.
- The key in this area is to decide how it is going to pass through the wing socket area and king post - this will vary depending on your design
Assembly:
- Now that you have your front assembly ready to fit to boat, make any adjustments you need to do to the full bulkhead that will sit underneath the sockets. This is your last chance before you glue onto it.
- Set the sockets into the hull, slot all the wing frame together, then glue the front and rear sockets plus anything else that is in these areas into place.
- Next glue in your bulkhead under the front / rear sockets and transom.
- Glue in the main foil case and supports - make sure it's vertical!
- Around this point you will need to add in the mainsheet attachment points and the gantry reinforcement.
- All the joins need to be carboned into place. I use on layer of biax and one plain on each join to help hold each bulkhead and support in place (3x more on the foil case to hull).
Deck: (not needed on a solid wing as your wings will cover the deck area)
Keep it flat, keep it simple!
- For your tramp bolt rope you will need to cut away enough of the outer carbon and foam from the top of the hull to glue a tube down each side of the boat between the wing sockets.
- Lay a piece of foam on the top of your hull. Draw around the foil case which should be sitting proud of the hull as you made it long, and anything else that may stop it sitting flush with the hull.
- Cut this out and slot it back over the case so it now sits in the hull.
- Draw around the hull and cut out.
- Decide where you are going to add reinforcement into your hull and deck - i.e. where you want to screw fittings. Cut the foam away in these areas and glue carbon plates or G10 in their place.
- Sand the deck edges down so that they match the boat perfectly.
- Get a large flat board and cover in release tape and agent. Wet out a piece of 200g plain weave on the board, wet the top of the deck foam and lay foam board on top on top of the plain weave. Wet the bottom of the foam and lay 200g biax on that. Lay Peel Ply on top of all the exposed carbon and then vacuum bag it.
- Test fit the deck again to make sure it is still a good fit.
- When happy glue in place.
Bow / Nose Cone Area:
- Ensure all bulkheads are taped into the hull and that pushrod tube is well bonded on (unidirectional carbon wrapped over and down the bow) and supported if you have run the bowsprit / forestay from it.
- Shape a piece of foam insulation to the required mould shape (likely a cone) and lay up as you did the hull.
- Trim the cone and hull so that the cone will slot into the hull. You may want to remove the outer layer of carbon from the cone and the inner layer of carbon and foam from the hull.
- Once determined a good fit, glue in place.
Finalising The Hull:
- Where you have glued the deck to the hull this needs to be taped 200g +/- 45 biax x2 layers and 2x plain weave alternately, then left to vacuum and set.
- (For removable wings, a groove needs to be cut into the tramp bolt rope tube so that it is useable).
- Nose cone needs two layers of carbon - one Biax and one plain over the join to the hull.
- You will now need to post-cure your hull - build an insulation oven and use heaters to gently raise the temperatures (see the resin manufacturer's data sheet - I did this in my living room).
Finishing Overall:
- Fill / sand (there will be lots of this).
- Paint.
Other things to build:
The gantry should be no more than 500mm from the back of the boat to the furthest point of the gantry (this is a class rule).
- Standard gantries are made from tubing and are very strong and simple. Make a jig to hold your tubing in the correct place, glue them and then wrap with carbon around all the joints.
- You can also make a solid gantry as you would the hull, but you need to ensure that it is not buoyant to comply with class rules.
Prodder:
- Cut the prodder shape out of some foam - I used the same as my hull foam. Shape the top of the prodder so that all the sides taper down to the bottom.
- Where the prodder is going to fit to the mast, add a piece of solid carbon thick enough to be drilled and tapped for an eye bolt to be screwed in.
- Cut the ends of your foam prodder where your shrouds will eventually slot, and add carbon plate here.
- Cut strips of carbon to go down the arms of the prodder. I did enough so I had one two layers of uni directional down the arms and a plain on top. This may be quite a lot but it has never broken (fingers crossed).
- Wet out the bottom layers of carbon and the prodder. Layer it all onto a flat board, cover in tape and release agent, then wet the top of the prodder and lay the rest of the carbon on top.
- Vacuum this all down onto the board.
- Once set, drill and tap the point for your eye bolt.
- Drill the holes in the end of your prodder arms for the shrouds and forestay.
Bowsprit, Wand Mechanism, Control system
The control system is one of the most important bits on the boat to make it easier to sail in most conditions. You can either buy systems from manufactures and adapt them to fit your design or build from scratch. Ensure that:
- There is little to no play in any of the joints you make.
- If you glue any inserts into your control tubes, wrap over them with carbon - they do have a habit of pulling out
- Ensure you get full flap movement on your foil.
- Any gearing adjustment from the deck to the pushrod that is linked to the bell crank must be on the same pivot point as the bell crank pivot itself. If not your gearing will be continually adjusting itself with the movement of the pushrod.
- Having a lot of adjustment is good in your wand and push rod, as it will help to set the boat up once sailing.
Control lines:
Before drilling and fitting any hardware to your new boat, make sure you know exactly what controls you are going to have. If you do not plan this your controls will look messy and also not run freely of each other. Tape out where everything is going to run. Put the hardware on the deck - I use electrical tape to see where ropes are going to snag others, or where friction points may be. Once you are happy, then start adding the hardware. Rig one thing at a time and make any adjustments you may need along the way.
Rig:
Decide what you are going to use for your shrouds. I use rope rather than wire as this is easily adjustable especially while setting the boat up.
- Use some old rope to start with to tie your mast up in the air - this way you can take measurements for rough shroud and forestay lengths.
- You can then make the top hound attachments, work the lower attachment points from your rough measurements, and set your mast rake to where you want it.
I hope this has been useful or at least an interesting read. As I said, this is how I have made my boats and they have been great and taken me to some amazing places. There is nothing better than beating people round the course or going over 30 knots in your own home-built boat.
It is a large task - don't be fooled - but it is the most rewarding thing I have ever done and I look forward to doing the next one!