CNC Spar Production at Selden Masts: Faster and more consistent
by Mark Jardine 25 May 2017 13:00 BST
25 May 2017
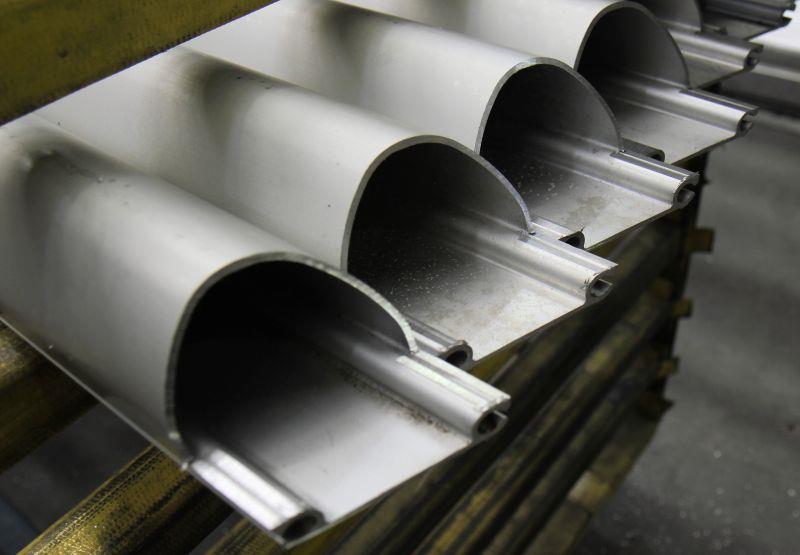
Cut extrusions at Selden Masts © Mark Jardine
We recently spoke to Steve Norbury about Selden Masts' new tool which is used for many of the mass-production extrusions which need repeated and extremely accurate cutting and hole positioning. Investing in a custom CNC machine has dramatically reduced production time for these parts.
"One of the driving reasons for investing in this machine was that we needed to reduce the amount of time that it was taking for sawing, drilling and cutting aluminium tubes. One of the new requirements at Selden is making beams for catamarans, like the Dart 16 and RS Cat 16 and also monohulls such as the RS Quest and the Laser Bahia. Typically with a Laser Bahia cross-beam we could make about four in a day, by hand. With this machine we can make one in 2 minutes and 30 seconds."
Even with the best machinist in the world there are always tolerance issues, but the CNC cutter makes repeatability extremely accurate as Steve explains:
"The tolerance is much better on the machine. While the advantage for our OEM (Original Equipment Manufacturer) customers is the output we get, for the racing sailor it's the accuracy in the position of fittings. A typical problem for a dinghy sailor might be that they put their mast in the boat and the mast for some reason doesn't quite sit straight side-to-side. One reason for that can be that the T-terminal positions for the cap shroud, when put in with a hand router, are accurate to within around +/- 0.5mm. With our CNC machine we're accurate to within 0.01mm, so for the racing sailor there is a benefit that their cap shrouds, forestay position and spreader brackets will be far more accurate than was previously achievable by hand."
Improved mass-production is now possible for the OEM market, and Selden are now putting through large batches for the major manufacturers:
"With the OEM work it has completely changed the way that the factory operates. Previously the cutting of the tube to length, the drilling of the holes, the routering of the T-terminal positions and the fittings placement was all one operation. In order to keep batch sizes manageable we would look at a sales order that might be for 25 masts and we would make 25 complete tubes in one operation with the assembly. With this machine it's much more efficient to do all of the cutting, drilling and routering in one hit. We'll take a batch of tubes, maybe 100, 150 or 200 tubes, and we'll run those through in a day and then put the fittings on at a later date as the sales orders require."
This investment delivered a step-change in what Selden are able to do for OEM customers and provided the ability to deliver even higher quality spars:
"We've been looking for a machine like this for a long period of time: about 10 years. We needed one that could drill, cut and router an oval-shaped, tapered tube. Despite all the advances in robotics and CNC equipment it was actually very hard to find a machine that could do that and also drill holes 360 degrees around the tube. It was only by working with the machine supplier and developing some special tooling that we've managed to get this machine, which will go all the way around the tube. The investment has been high, but we believe it's an essential tool as we continue to expand and refine the quality of our product."
www.seldenmast.co.uk