The Aluminium Cocktail: what goes into the perfect mast
by Mark Jardine 3 Oct 2016 13:13 BST
3 October 2016
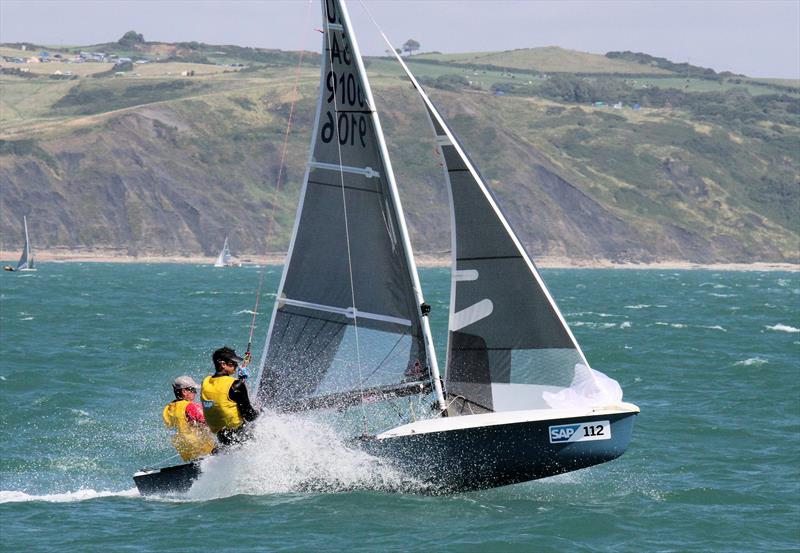
Mike Martin & Adam Lowry win the 2016 505 World Championship using the Selden Alto mast section © Mark Jardine
While carbon is the 'sexy' material of choice for spars, aluminium accounts for a far greater proportion of the masts and booms used in sailing and is much cheaper. What goes into an aluminium mast, and the processes to consistently produce a good spar, though are far from simple - like a good cocktail, the mix of ingredients and the production processes are vital. We spoke to Selden's Steve Norbury and Andy McCormack to find out more...
Firstly we talked to Steve about aluminium itself and where masts sit in the different 'series' available to a manufacturer.
"Over time masts have been made from quite a different number of series of aluminium, all to have different properties. The series of aluminium that is mostly used for mast manufacture, and what we use is 6000 series. The 6000 is relatively hard, extrudes well, is heat treatable and has good corrosion resistance. This means that we can buy them in a soft condition so that we can work with them, and then heat treatment brings them up to full strength. So overall, 6000 series aluminium is reckoned to be the best to make dinghy and yacht spars from.
"There are other families; the 2000 series is a copper-based aluminium and is also very strong. You would think they would make ideal masts, but unfortunately, they have terrible corrosion resistance. If you stored your mast in a bag, maybe for the Winter, you would literally open up that bag in the Spring and find that you had a pile of white powder!
"Another series which is used, is 7000 series. 7000 series has the advantage over the 6000 series in that its yield point is high. That means it is a very strong metal that you can bend further without it taking a permanent set. The disadvantage is that it is almost impossible to work with. You can buy 7000 series round tube, but you can't get profile section, you can't taper it, you can't weld it, and again it has a corrosion problem in that after a few years you would find that your fittings start corroding. So it has been used for windsurfing masts and used for some Optimist spars, but, generally for dinghy spars 6000 is the best material that you can use."
Andy McCormack is Technical Director at Selden and we asked him how you go about extruding a mast into a particular section.
"We have a range of sections, seven or eight, covering the entire dinghy range; some of them are very close together. Cumulus is our most popular section, we also have another section called Alto which is very slightly stiffer, and one called Zeta, which is slightly more flexible - they are very, very close together. Due to the volume of aluminium that we buy, we are able to have three separate dies, that are discrete sections, but very, very close, just a few percent stiffer or more flexible each way."
With this range of sections, and having masts that are very similar in their characteristics, we wanted to know how they could ensure repeatability, managing to produce the same mast each time. Andy explains:
"Due to the volume of aluminium extrusions that we buy, we have a tighter set of tolerances that we have agreed with our supplier. Rather than using a British Standard or ISO Standard, we have a Selden Spar standard, which governs overall dimensions, wall thickness, straightness, material properties, and this standard is much tighter than commercially agreed standards that other people may use."
The next problem for repeatability is when a mast section is tapered. This requires a cut and weld in a spar and we wanted to know how they kept the same mast characteristics each time. Andy told us about the technology Selden use to improve consistency:
"Rather than cutting the taper by hand, we have a plasma cutting machine, essentially a CNC machine, cutting a section out of the top of the mast, very accurately and consistently.
"We then press that together on a custom tooling for each section. After that the taper is welded on an auto welder - again, this is the same every time. This results in very tight tolerances and is completely repeatable; there is no human intervention.
The final stage of creating a mast is having it heat-treated and then anodized. Andy explains how Selden go about this process:
"We have our own heat treatment oven that is computer controlled with sensors clipped to mast tubes. This produces a graph of the heat cycle for every run. This way we can be certain that the material in the oven has been correctly heat treated.
We carry out a peening operation which gives us a uniform surface finish, it also removes any impurities off the surface of the material. That allows us to send it for anodizing in a state where they have to do the absolute minimum of cleaning and etching, meaning there is no further reduction in material before the anodizing is put on."
Like all industries and companies, aluminium spar making is moving on, and Selden are at the forefront of experimentation and innovation. We asked Steve what changes are in the pipeline:
"We are all always working with our extruder to develop new modifications to this, or new blends if you like. We are working on some material now, which gives us a much higher yield point - for a dinghy sailor means that a mast will bend further before taking a permanent set. So while we are trying to improve that, we are also trying to retain its surface finish and its anodizing properties."
Finally we wanted to dispel some myths about aluminium masts, particularly with regard to bend and gust response. Steve explained the facts to us:
"Gust response is all about when a gust hits, the masts bends, and when the gust disappears, the mast bends back. It is all about the stiffness of the material, the weight of the material, and pretty much nothing else. If you look at the formula, it's the stiffness of the material which is the most important factor.
With aluminium there are very marginal differences in stiffness. But there are massive differences in their yield point - the point you can bend something to before it takes a permanent set. So aluminium masts are all the same stiffness, but they could have a different yield point."
Selden are the biggest spar manufacturer in the world and work closely with their extruder on experimenting with the 'mix' in their masts. It is the volume of work that gives them the flexibility to do this as Steve explains:
"All our dinghy sections come from one extruder and we use many more tonnes of aluminium a year, making us a big enough customer to work with to develop spars with new proprieties. We can make a trial run of a section in a particular material, whereas I doubt they would do that for some smaller manufacturers."
www.seldenmast.co.uk